Take Full Advantage Of Performance: Proactive Pipeline Welding Inspection Methods
Take Full Advantage Of Performance: Proactive Pipeline Welding Inspection Methods
Blog Article
Crucial Pipe Welding Inspection Tips for Quality Control
In the realm of pipe building, the stability of welds holds critical significance to guarantee the safety and security and performance of the whole system. From natural gas to improved oil products, pipes develop the lifeline of different markets. Exactly how can one assure the quality of these welds that connect the pipeline sections? The response depends on careful examination techniques and adherence to strict high quality assurance requirements. By recognizing the crucial pipe welding inspection ideas, experts can avert possible hazards, reduce expensive fixings, and support the dependability of these vital infrastructures.
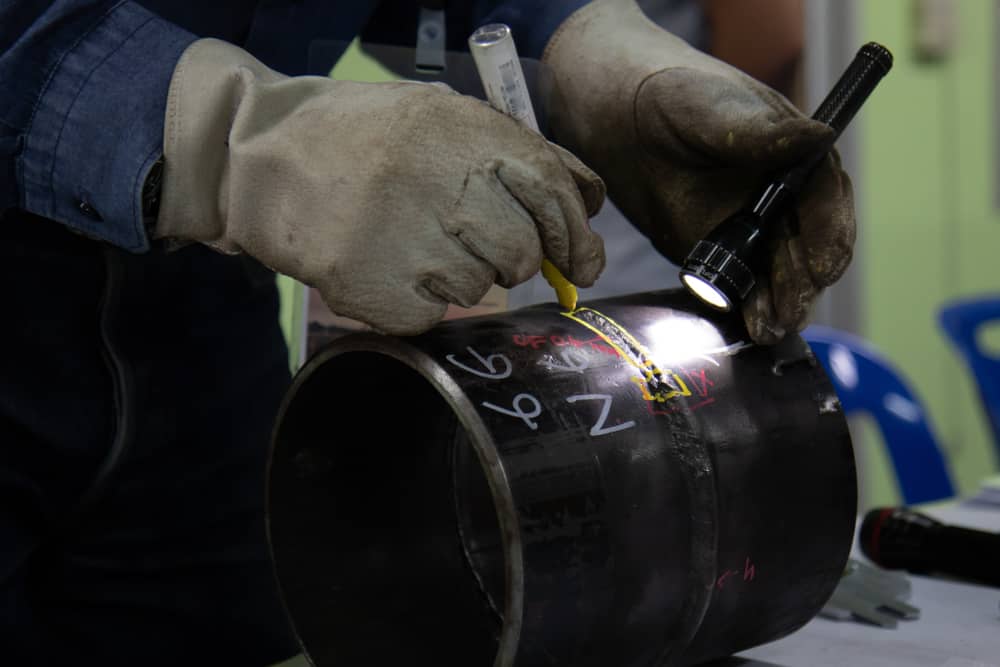
Importance of Welding Examination
Welding evaluation plays a critical role in guaranteeing the architectural stability and safety and security of pipeline systems. By thoroughly taking a look at welds, assessors can identify any kind of defects or flaws that could compromise the integrity of the pipeline. These assessments are necessary for protecting against leaks, tears, and other potentially disastrous failures that can result in ecological damages, monetary losses, and even death.
The relevance of welding inspection can not be overstated, as the high quality of welds directly impacts the overall efficiency and durability of the pipe. With non-destructive screening methods such as aesthetic examination, ultrasonic screening, radiography, and magnetic bit screening, inspectors can spot imperfections that may not be visible to the nude eye. By identifying and dealing with these concerns at an early stage, welding assessment aids to ensure that pipes satisfy industry standards and governing demands.
Inevitably, welding inspection is an essential facet of top quality assurance in pipe maintenance, building, and repair work (Pipeline Welding Inspection). By upholding extensive inspection criteria, market specialists can minimize dangers and maintain the security and dependability of pipeline systems
Common Welding Flaws
Among the difficulties dealt with in pipe welding, usual flaws can dramatically impact the structural stability and efficiency of the bonded joints. Cracks in the weld can circulate over time, jeopardizing the structural stability of the pipeline. Finding and resolving these usual problems with complete assessment and top quality control processes are essential for making certain the reliability and safety of pipe welds.
Examination Techniques for Pipelines
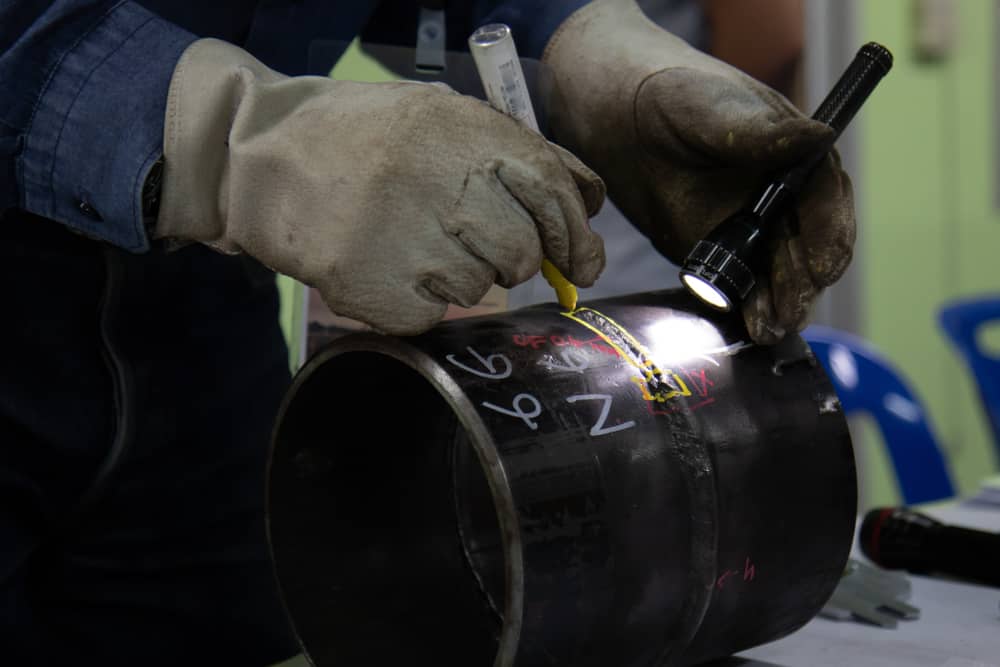

Non-destructive testing (NDT) techniques such as radiographic testing, ultrasonic testing, magnetic particle screening, and liquid penetrant screening are frequently used in pipe welding inspection. Aesthetic assessment is likewise necessary in pipe welding to determine any kind of visible problems or stoppages. In addition, automated assessment techniques utilizing advanced modern technologies like robotics and drones are increasingly being utilized to enhance the effectiveness and precision of pipe evaluations.
Ensuring High Quality Assurance Requirements
To promote rigid high quality assurance criteria in pipe construction, thorough adherence to established market procedures and guidelines is necessary. Quality guarantee in welding procedures needs a detailed technique including different phases of pipeline construction. Applying a durable top quality administration system that includes regular audits and evaluations can further enhance the overall top quality assurance requirements in pipeline welding.
Protecting Against Costly Repairs
Offered the important relevance of maintaining stringent quality assurance criteria in pipe important source building and construction, a positive technique to stopping expensive repair services is important. Regular upkeep checks and monitoring of ecological factors that could influence the stability of the pipe are also essential in stopping costly repair work. By investing in preventative measures and focusing on top quality assurance at every stage of the pipe welding process, business can minimize the danger of expensive repair work and ensure the long-lasting dependability of their facilities.
Conclusion
In verdict, adherence to appropriate welding inspection techniques is vital for making certain the top quality and stability of pipelines. By identifying common welding issues and applying thorough assessment processes, expensive repair work can be stopped, and quality control standards can be met - Pipeline Welding Inspection. visite site It is vital for pipe welders to prioritize examination procedures to maintain the safety and integrity of the framework they are working on
The significance of welding assessment can not be overemphasized, as the quality of welds straight influences the overall performance and durability of the pipe. Non-destructive screening (NDT) methods such as radiographic screening, ultrasonic testing, magnetic particle screening, and fluid penetrant testing are frequently utilized in pipe welding inspection. Visual assessment is likewise important in pipe welding to recognize any type of noticeable defects or gaps. In addition, computerized examination strategies utilizing advanced technologies like drones and robotics are progressively being utilized to improve the performance and accuracy of her comment is here pipeline inspections.In verdict, adherence to appropriate welding assessment methods is crucial for ensuring the top quality and stability of pipes.
Report this page